MotocPS 2.0 represents a significant advancement in motor control technology. It is a sophisticated motor control power supply system designed to optimize the performance, efficiency, and reliability of electric motors, particularly in applications such as electric vehicles (EVs), robotics, and industrial systems.
The evolution of MotocPS from earlier versions has brought improved capabilities in energy management, fault tolerance, and integration with cutting-edge technologies like AI and machine learning. This guide provides a comprehensive look at MotocPS 2.0, from its key components to its future prospects.
1. Introduction to MotocPS 2.0
What is MotocPS 2.0?
MotocPS 2.0, short for Motor Control Power Supply 2.0, is an advanced system that integrates both hardware and software components to control and power electric motors with exceptional precision. This system ensures optimal motor performance by regulating power flow, adjusting motor speeds, and managing the system’s energy efficiency. Its significance lies in its ability to provide real-time motor control, which is essential for applications ranging from electric vehicles to industrial robots.
MotocPS 2.0 builds on its predecessor by offering greater flexibility, higher processing power, and better integration with modern communication protocols. As electric vehicles (EVs) become more mainstream and industries push towards automation, MotocPS 2.0 is playing a pivotal role in ensuring the reliable operation of high-performance electric motors.
2. Key Components of MotocPS 2.0
The core strength of MotocPS 2.0 lies in its design, which combines various advanced components working together seamlessly. The following are the key components that define its functionality:
2.1 Motor Control Algorithms
At the heart of MotocPS 2.0 lies the advanced motor control algorithms that manage the electric motor’s operations. Some of the key algorithms include:
- Field-Oriented Control (FOC): This algorithm is used to control the torque and flux in the motor, enabling smoother and more efficient operation. It provides superior performance in terms of responsiveness and efficiency.
- Direct Torque Control (DTC): DTC is an advanced method that controls torque directly, reducing the time response of the motor and enhancing performance, especially in variable speed applications.
- Pulse Width Modulation (PWM): PWM controls the voltage and frequency supplied to the motor, offering precise control over the motor speed and torque.
These algorithms work together to ensure that the motor performs at its peak efficiency, minimizing energy waste and optimizing response times.
2.2 Power Supply Systems
MotocPS 2.0 integrates a sophisticated power supply system, which includes power inverters that convert DC (direct current) from the battery to the AC (alternating current) required by the motor. This ensures the motor operates smoothly and consistently. The system also includes mechanisms for battery management, ensuring that the power supply remains efficient and that the battery’s lifespan is extended by preventing overcharging or deep discharge.
2.3 Sensors and Feedback Systems
For precise control, MotocPS 2.0 utilizes various sensors and feedback systems. These include:
- Position Sensors: These sensors provide real-time data on the rotor position, which is essential for effective motor control.
- Temperature and Voltage Sensors: These sensors monitor the motor’s operating conditions, ensuring it doesn’t overheat or experience voltage spikes that could damage the system.
2.4 Communication Interfaces
Communication between different components in MotocPS 2.0 is facilitated by interfaces such as the CAN Bus. This system allows real-time data transfer between the control unit, sensors, and other components, enabling efficient diagnostics and troubleshooting.
3. Architecture of MotocPS 2.0
3.1 System Architecture Overview
The architecture of MotocPS 2.0 is designed to be both robust and scalable. It consists of a control unit, power management systems, and communication channels. The heart of the system is the Motor Control Unit (MCU), which processes sensor data and executes the motor control algorithms.
The system also includes power converters and inverters that regulate the power supplied to the motor. This ensures that the motor runs efficiently across various operating conditions, whether it’s starting up, accelerating, or decelerating.
3.2 Control Unit
The control unit of MotocPS 2.0 is equipped with powerful microcontrollers and digital signal processors (DSPs) that handle complex computations in real-time. These components are crucial for the precision and speed of motor control operations. The control unit processes inputs from sensors, executes the motor control algorithms, and manages power delivery.
3.3 Modular Design and Scalability
MotocPS 2.0 is designed with scalability in mind, which means it can be adapted to suit different types of motors, such as AC motors, DC motors, and brushless DC motors (BLDC). Its modular design allows it to be customized for specific applications, from compact e-bikes to large industrial machinery.
4. Features and Benefits of MotocPS 2.0
MotocPS 2.0 is packed with features that make it ideal for modern motor control applications. Some of the standout benefits include:
4.1 Enhanced Performance and Efficiency
One of the main advantages of MotocPS 2.0 is its ability to optimize motor performance. By using advanced control algorithms like FOC and DTC, it delivers superior torque efficiency and precise speed control. This results in reduced energy consumption and longer battery life in electric vehicles and other portable applications.
4.2 Advanced Diagnostics and Monitoring
MotocPS 2.0 has built-in diagnostics features that monitor the system’s health. It continuously tracks variables like motor temperature, voltage levels, and torque output, providing real-time feedback to prevent potential failures. In the event of an issue, the system can alert the user and suggest corrective actions.
4.3 Improved Safety and Reliability
Safety is a primary concern in electric motor systems, and MotocPS 2.0 has been designed with this in mind. It includes protection mechanisms such as overcurrent and overvoltage protection, thermal monitoring, and fault detection. These features not only extend the lifespan of the system but also enhance its overall reliability.
4.4 Scalability and Flexibility
MotocPS 2.0’s modular architecture makes it highly flexible. It can be adapted to various motor types and applications, making it an ideal solution for industries ranging from automotive to robotics and beyond.
5. Applications of MotocPS 2.0
MotocPS 2.0 is versatile and can be applied across numerous industries. Here are some of its key applications:
5.1 Electric Vehicles (EVs)
MotocPS 2.0 plays a crucial role in optimizing the performance of electric vehicles. By efficiently controlling the motor’s power output and integrating with the vehicle’s battery management system, it enhances the driving range and reduces energy waste. This is vital as the automotive industry transitions to fully electric solutions.
5.2 Electric Bicycles and Scooters
In e-bikes and electric scooters, MotocPS 2.0 provides compact and lightweight control systems that ensure smooth and efficient motor operation. Its ability to regulate power delivery is essential for achieving a balance between performance and battery life in small, battery-powered vehicles.
5.3 Industrial Applications
MotocPS 2.0 is also widely used in industrial systems, including robotics and automated machinery. Its precision control ensures that motors in robotic arms, conveyors, and other machinery perform optimally, enhancing production efficiency and reducing operational downtime.
5.4 Marine and Aerospace Applications
In industries such as marine and aerospace, where reliability and performance are critical, MotocPS 2.0 provides the necessary power control to ensure smooth operation of electric propulsion systems, reducing fuel consumption and enhancing environmental sustainability.
6. The Future of MotocPS 2.0
Looking ahead, MotocPS 2.0 is set to evolve further. The integration of artificial intelligence (AI) and machine learning will allow the system to predict failures before they occur, enabling preventive maintenance. The use of wide bandgap semiconductors like silicon carbide (SiC) and gallium nitride (GaN) will improve power efficiency, especially in high-voltage and high-frequency applications.
Conclusion
In conclusion, MotocPS 2.0 is a game-changing system that significantly improves the efficiency, performance, and reliability of electric motor-driven applications. Whether it’s used in electric vehicles, industrial automation, or robotics, the system’s advanced features make it a cornerstone of the future of electric motor technology.
As industries continue to embrace electrification, MotocPS 2.0 will remain at the forefront of motor control innovations, driving the future of energy-efficient, high-performance systems.
Frequently Asked Questions (FAQs) About MotocPS 2.0
1. How does MotocPS 2.0 support energy regeneration in electric vehicles?
MotocPS 2.0 supports energy regeneration by managing the regenerative braking system in electric vehicles (EVs). During braking, the motor acts as a generator, converting kinetic energy back into electrical energy, which is then stored in the battery. MotocPS 2.0 ensures that this process is efficient, adjusting the motor’s operation to maximize energy recovery without overloading the system. By doing so, it extends the vehicle’s driving range and improves overall battery longevity.
2. What are the power consumption benefits of using MotocPS 2.0 in industrial robots?
In industrial robotics, MotocPS 2.0 optimizes motor control to reduce power consumption by ensuring that motors operate only when necessary and at optimal power levels. By dynamically adjusting motor speed and torque based on real-time load demands, it minimizes energy waste. This leads to more efficient operations, lower operational costs, and an overall reduction in the energy footprint of industrial automation processes.
3. Can MotocPS 2.0 be customized for specific motor types?
Yes, one of the significant advantages of MotocPS 2.0 is its modular design, which allows for customization based on the specific motor type. Whether you are using AC motors, DC motors, or brushless DC motors (BLDC), MotocPS 2.0 can be tailored to meet the requirements of each. Its scalability makes it ideal for a wide range of applications, from low-power electric bikes to high-power industrial machinery.
4. What role does MotocPS 2.0 play in reducing the environmental impact of electric vehicles?
MotocPS 2.0 contributes to reducing the environmental impact of electric vehicles by improving energy efficiency. It ensures that the electric motor operates at peak efficiency, minimizing energy waste and extending battery life, which in turn reduces the frequency of battery charging. Additionally, its ability to manage regenerative braking means that energy that would typically be lost is captured and reused, further enhancing the vehicle’s sustainability.
5. How does MotocPS 2.0 handle communication between different vehicle subsystems?
MotocPS 2.0 integrates seamlessly with other subsystems of an electric vehicle, such as the battery management system (BMS), the vehicle control unit (VCU), and the motor controller. It uses industry-standard communication protocols like CAN Bus to ensure smooth and reliable data exchange between these subsystems. This coordination is vital for optimizing the vehicle’s performance, ensuring that the powertrain and other systems work harmoniously, adjusting to real-time driving conditions for improved efficiency and safety.
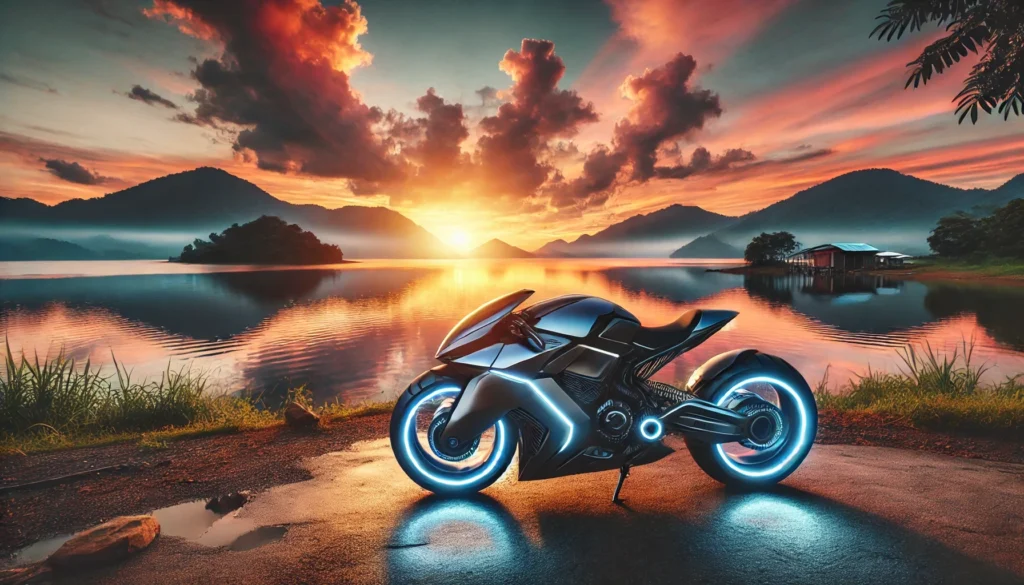
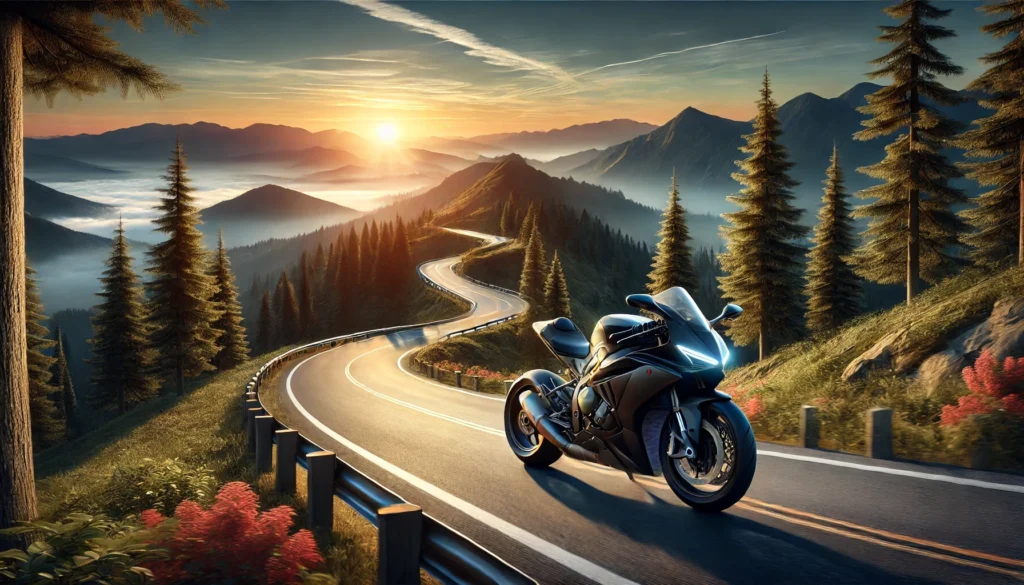